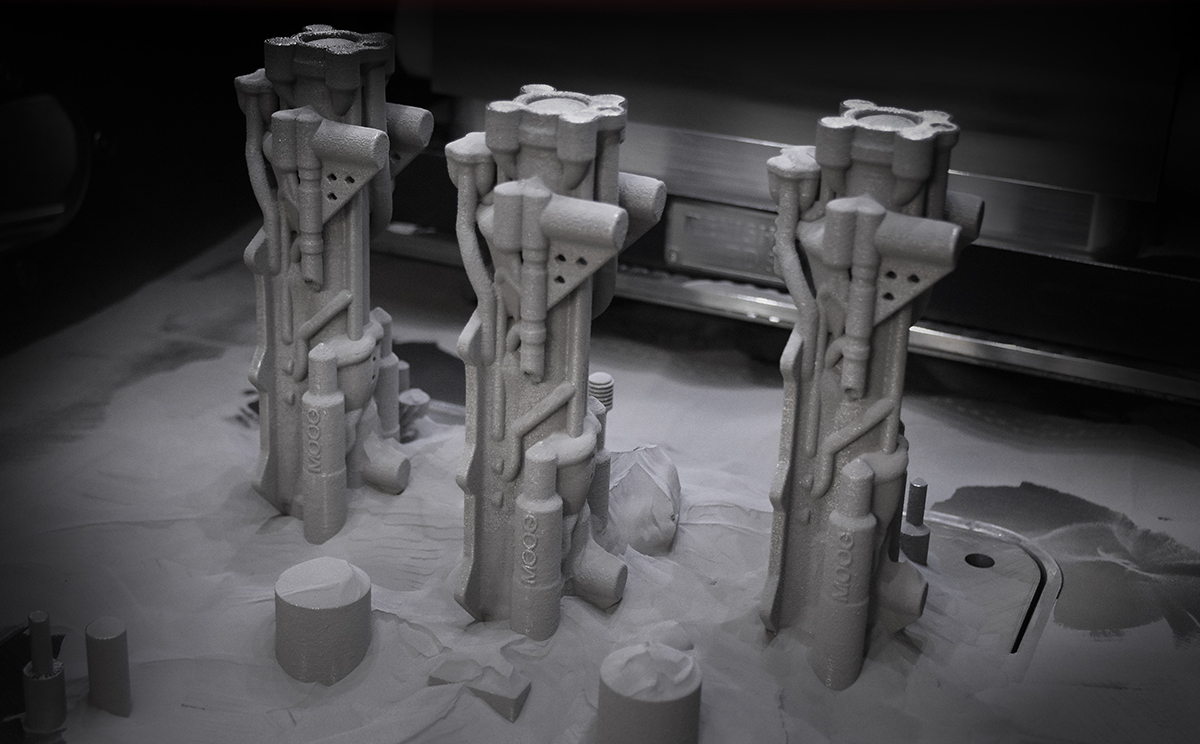
Moog joins in development AM industry standards
Manufacturing parts with additive (3D printing) equipment at production rate and scale will require the acceptance of industry standards for raw materials, processing, and qualification. This prerequisite will vary by industry and application, but in every case where an additive solution is adopted for production, designers and engineers will require standards that can be referenced and against which end-use articles can be verified.
We’ll consider here five different organizations that are at work in the development of industry standards, look at Moog’s involvement with these groups, and explain how these may apply to parts that you are considering for additive manufacturing.
Moog has been heavily involved in the development of these standards for a number of years, giving the company a leg up on complying with them and being able to reference them confidently on drawings and other required documents.
1. NASA Marshall – NASA’s Marshall Space Flight Center has released two documents. The first, MSFC-STD-3716 (“Standard for Additively Manufactured Spaceflight Hardware by Laser Powder Bed Fusion in Metals”) deals with controls for specific pieces of spaceflight hardware. The second, MSFC-SPEC-3717 (“Specification for Control and Qualification of Laser Powder Bed Fusion Metallurgical Processes”) pertains to control of the laser powder bed fusion additive manufacturing (LPBF-AM) process. Moog has written compliance matrices to both specifications.
2. AMS 7003 – This is a standard crafted by the Society of Automotive Engineers (SAE) for its Aerospace Material Specifications database. The purpose of the specification is to standardize the production of aerospace parts via the laser powder bed fusion (LPBF) process. As with the NASA Marshall specs, Moog has produced a compliance matrix for AMS 7003. While the Additive Manufacturing Center in Plant 11 has yet to produce a part governed by this standard, it has quoted projects whose drawings call for compliance to it. Moog collaborated with SAE in the initial drafting and revision of the specification through SAE’s Industry Technology Consortium (SAE ITC), a neutral body that gathers industry input at a pre-competitive stage to set standards industry-wide. In addition to helping draft specifications, Moog has shared data from tensile and fatigue testing of Ti64 coupons with SAE.
3. ASTM International - The organization, formerly known as American Society for Testing and Materials, is developing its own set of standards for additive manufacturing. These cover design, manufacturing, terminology, and testing methods. Among the better known of its standards is F2924-14 for the manufacture of Ti64 additive parts. Moog has reviewed a number of ASTM specifications for compliance. One key customer has called out F2924-14 on a recent RFQ.
4. AWS – The American Welding Society is also engaged in the development of AM standards and Moog is currently writing a compliance matrix to its D20.1/D20.1M:2019 (“Standard for Fabrication of Metal Components using Additive Manufacturing.”)
5. MMPDS – the Metallic Materials Properties Development and Standardization Handbook provides a guide to material properties and design allowable values for a vast array of alloys. At present, MMPDS is working to create a new volume of its handbook series that will cover additive manufacturing. The working group tasked with writing the volume includes three subcommittees: data generation and applications; materials and machines; and certification and qualification. The last subcommittee is co-chaired by Moog’s own Dr. Paul Guerrier, the director of the Additive Technology Center in Plant 11. Because of its high-level of involvement in the MMPDS effort, Moog has a deep understanding of what flight qualification of AM parts will entail and what data will need to be generated. Moog is necessarily in regular communication with regulators (from FAA et al).
The flurry of activity in standards development reflects a growing interest in using additive manufacturing for novel solutions to engineering problems in end-use components. AM will continue to play a role in prototyping though production parts will be increasingly manufactured. Engineers and designers will place their confidence in additive parts to the extent that they see their fabrication being governed by standards. These standards are being developed to a considerable degree with input from Moog. The company has been an early and leading adopter of the technology and its involvement with the generation of standards means that it has an edge in the development of additive parts for end-use production across the markets in which it competes. To learn more about the status of compliance to the standards above, please reach out to us.