Why should a hard-working engineer worry about trends in hydraulic motion control, especially in challenging economic times? Smart engineers know that there is always more to learn from others who are facing similar challenges. Industry associations play an important role in bringing together people who are on the front lines of both issues and challenges facing machine builders. This article explores some trends identified by the National Fluid Power Association (NFPA), headquartered in the United States, that recently brought together a team to articulate a Technology Roadmap for the fluid power industry. Having the advantage of working with many companies in some of the world’s most demanding industries, Moog has vast experience developing solutions that address these trends. Electro-hydrostatic systems are a technology area emerging in industrial applications and Moog is looking at it as a promising solution for addressing all of the tough issues identified by NFPA.
The NFPA in May of this year asked its members to develop a technology roadmap for the next decade addressing six challenges facing the industry. One motivation behind the NFPA technology roadmap is a realization that the industry has to change to face threats from electromechanical solutions that are increasingly encroaching on the fluid power industry’s core business, such as power generation and sub-sea drilling applications. As the NFPA and its members see it, the six challenges for the fluid power industry are:
Six Challenges for the Fluid Power Industry
- Increasing energy efficiency
- Improving reliability
- Building smart components and systems
- Reducing size and weight
- Reducing environmental impact
- Improving and applying energy storage and redeployment capabilities
Source: NFPA Website Dec. 09.
Visit www.nfpa.com/ourindustry/technology_roadmap.asp (link updated May 2013)
There are many implications for designing new hydraulic products and systems that can be considered from these challenges. For example, improving reliability can be accomplished by developing smaller, self-contained hydraulic systems with far fewer components. Size and weight can be reduced by designing a solution optimized for the application. Energy efficiency can be increased by designing a motor rotating only when movement is required and smart components allow greater customer interaction.
A Practical Look at Addressing the Big Six
As Moog is a leader in the design and manufacture of hydraulic solutions and products, we have been a member of the NFPA for many decades. I was selected to represent our company as Moog has an interesting perspective on the topic. We are known for being “technology-neutral” and are one of the few companies that design both hydraulic and electric solutions. Literally, our electro-mechanical and electro-hydraulic teams sit in adjacent cubicles. Every day, these teams see the advantages and disadvantages of hydraulic systems and their competing electro-mechanical solutions, across a wide range of applications as diverse as steel mills and aerospace testing.
For each of these trends, our engineers have a fascinating story to tell. For example, as described in Challenge #1 plastic injection molding machine manufacturers have been enjoying greater energy efficiency using the Moog Digital RKP-II (Radial Piston Pump). One of the most high force hydraulic applications, needing extreme reliability for 24/7 operations are automotive test labs that perform structural testing of the latest auto component prototypes. Moog recently introduced a rugged, compact servoactuator for this market that exactly meets the need identified in Challenge #2 with its compact, self contained piping and special seal-rod technology for a long service life. In this market, Moog also developed a simulation table for automotive R&D testing with a hexapod 6 Degree of Freedom design that has a much smaller footprint and reduced weight yet it can attain higher frequencies than traditional solutions (See Challenge #4).
Smart components, addressed in Challenge # 3, are the area where Moog has invested extensive R&D and application resources. Moog has a range of Digital Servovalves and Digital Radial Piston Pumps that offer the opportunity for customers to use our Advanced Configuration Software to optimize performance, perform diagnostics and provide easier set-up. In addition, there are many examples where Moog offers customers biodegradable fluids and closed-hydraulic systems that are even suitable for clean-room medical manufacturing (See Challenge # 5).
Moog D637 and D670 Servovalves, Digital Radial Piston Pump
Emerging Opportunities with Electrohydrostatic Actuation
For the hydraulics industry and, ultimately, customers who seek high-performance systems for some demanding applications Electrohydrostatic Actuation (EHA) addresses the six challenges listed above and so warrants a discussion. EHA is sometimes known as “powered by wire” as actuation can be provided in a self contained unit combining both electric (e.g. servomotors) and hydraulic (e.g. pumps and valves) with a common controller and software system. The self-contained package has the advantage of no hydraulic piping required. The term hybrid technology is sometimes used for this technology as well.
Moog has extensive experience since 1990 with the use of EHA in flight controls for the next generation of military and commercial aircraft such as Lockheed Martin’s F-35 Lightning II and has been selected by Airbus for both the A400M and A350 XWB. Moog has spent the last two decades refining and maturing EHA technology for a variety of systems including simplex and dual redundant actuators, dual and triplex redundant actuator controllers and highly integrated designs with on-board power and control electronics.
While EHA is not typically used for industrial applications, Moog has begun working with OEMs with hydraulic applications that require high force requirements but also need for energy savings, environmental cleanliness or elimination of piping. EHA is also an option for electric applications that have high forces and require redundant or advanced fail-safe systems.
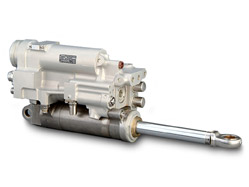
Moog EHA System for Aircraft
Conclusion
The NFPA’s roadmap is designed to advance fluid power technology and spur discussion of new options that can help the hardworking engineer facing today’s challenges. This article shared some ideas on practical ways these trends in hydraulics are being exhibited in high performance applications. As you can see there is an impressive range of hydraulic options including the emerging EHA option that can solve specific challenges in a variety of industries. Most importantly Moog offers the expertise to evaluate whether hydraulic or electric solutions are best suited to the needs of an application and then apply the best in class product or system to meet the needs of high performance machine applications.
The National Fluid Power Association (NFPA) is a 501(c)6 trade association founded in 1953. Its more than 300 members include manufacturers of fluid power systems and components, fluid power distributors, suppliers to the fluid power industry, educators and researchers. NFPA’s mission is to serve as a forum where all fluid power channel partners work together to advance fluid power technology, strengthen the fluid power industry, and foster member’s success. For more information visit www.nfpa.
Author
Dave Geiger is Hydraulic Systems Engineering Manager, Moog Industrial Group. He sits on the Technology Roadmap Team for the NFPA. His experience includes the design of motion control systems for plastics, metal forming, power generation, oil and gas exploration and automation machinery. He holds four patents with an additional three pending. He can be reached at dgeiger@moog.com.