In this article:
- Bi-axial material testing creates sophisticated control loops that reproduce stresses and strains in the test specimen
- The need for bi-axial testing for composite materials
- Moog Portable Test Controller's unique control loop technology
Mayes Bi-Axial Material Testing Machine
Material testing is a sophisticated motion control application. The high forces involved and the need to protect the test specimens are just two of the common concerns of virtually all test and structural engineers. And when it comes to testing composite materials, the risks become even greater.
At the University of Sheffield in the United Kingdom, engineers are focused on an application called bi-axial material testing using the Moog Portable Test Controller to create sophisticated control loops that reproduce stresses and strains in the test specimen. The tests are complicated and time-consuming, as the specimen has to be held in the absolute centre of the machine, so that the specimen loading is perfectly symmetrical to maintain the correct stress/strain distribution. Thus the choice of test controller is critical particularly when the equipment is used in a retrofit.
Moog has extensive experience in developing and applying servo controllers that are designed for specific applications such as testing materials, components and structures. The testing of materials can be complex for a number of reasons:
- Materials and components have complex loading patterns in the real world that must be approximated when testing.
- New materials have unique behaviors in service that need to be better understood before these materials can be incorporate in new applications.
- The move towards lighter, cheaper solutions means that mechanical testing has become more important in the development of next generation applications.
This article discusses bi-axial material testing where Moog’s Portable Test Controller was used as part of a retrofit by the University of Sheffield. The advanced features in the Moog Portable Test Controller allowed engineers to easily and expertly create complex control loops required in order to reproduce the stresses and strains in the test specimen.
Background
The Moog facility in Solihull, UK that focuses on Test and Simulation has worked with the University of Sheffield on several upgrades to their testing systems. The latest upgrade to a Mayes Bi-Axial test machine consisted of a complete overhaul of the machine and a new control system. The Bi-Axial machine uses a traditional cruciform fixture for testing various materials; such as steel, aluminium and composites. These materials are used in the nuclear industry, aircraft construction and civil engineering.
The test machine upgrade incorporated a four channel Moog Portable Test Controller. The complex control loops required for this customers’ test were configured using the advanced features and tools provided by the Moog system. This is the kind of flexibility and support which makes the Moog Portable Test Controller stand out from the competition, due to the reduced time required to configure the controller for different tasks.
Why Use Bi-Axial Testing?
As a result of extensive conventional testing, the behaviour of normal materials under multi-axial loads is well understood. However, the failure of new materials and some composites under multi-axial loading has been poorly understood, until quite recently. As industry uses more and more composites for critical applications ranging from aerospace to Formula One cars, it is necessary to understand the behaviour of these materials in service. In the real world materials normally experience loading in more than one direction at the same time, that is, they are bi-axial loaded. The work of the University of Sheffield and other organizations with the Mayes Bi-Axial Test Machine has helped to create of a large body test data backed by a theoretical understanding of the failure criteria that apply that can help increase the adoption rate of new composites in key industries.
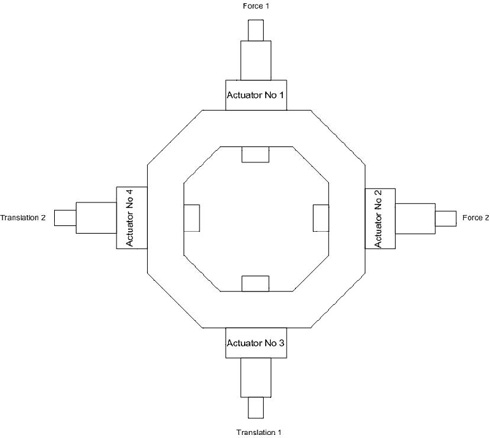
Bi-Axial Machine Configuration
What are the Challenges of Bi-Axial Testing?
The basic bi-axial test is called a cruciform coupon test and it can be used to measure basic material properties and study the strength of a specimen that includes specific features including open holes, loaded fasteners and impact damage sites. It is called cruciform as the test machine has a cross shaped plate as the test specimen.
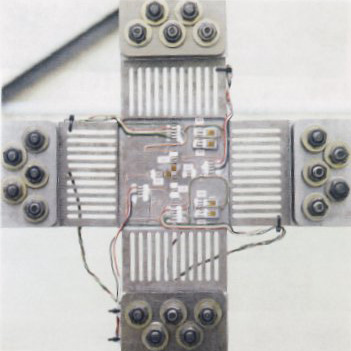
Specimen for Bi-axial Testing
Due to the inherently anisotropic (the property of being directionally dependent, as opposed to isotropy, which implies homogeneity in all directions) structure of some composite materials, their strength under normal bi-axial loading is dependent on how the loads are aligned with the fibre directions. If the applied loads are well aligned with the fibre direction then the specimen strength may exceed the value that may be obtained from simple uni-axial tests, making the bi-axial more representative of real world situations.
Bi-axial testing is notoriously complex because the specimen has to be held in the absolute centre of the machine, so that the specimen loading is perfectly symmetrical to maintain the correct stress/strain distribution. This means that the system needs to be controlled in both displacement and force, to ensure that the specimen is held perfectly centrally.
Using the Moog Portable Test Controller
The Moog Portable Test Controller incorporates a unique control loop technology to handle tests of up to 4 servo control channels. It can be used as a stand-alone controller or in conjunction with a PC. It was the ideal choice for the University of Sheffield due to its flexibility, high-performance handling of complex testing formulas and unique control loop technology for force, displacement and acceleration control.
Portable Test Controller
The Moog Portable Test Controller is used to control both displacement and force in bi-axial testing through the use of User Defined Channels and Pseudo Channels. Pseudo Channels are calculation channels which can be derived from transducer feedback and have mathematical functions applied to them to create control loop inputs, such as taking a force feedback and multiplying it by the distance of a loading arm to create a torque input.
The Pseudo or translation channels are used to keep the specimen perfectly centralized within the test machine frame. Additionally the user channels are used to apply the dynamic load to the specimen in perfect symmetry. Generally the dynamic force signals can be applied to both axes simultaneously.
Most importantly, the portable test controller is configured to allow easy switching between bi-axial control and conventional uni-axial control, which greatly reduces set-up and testing time.
Conclusion
Moog’s upgrade of the Mayes Bi-Axial Testing system that was completed last year also included the installation and calibration of the machine as well as the training of the University of Sheffield engineering staff. The incorporation of this application in the bi-axial machine brings the number of portable test controllers in operation to seven.
Mike Rennison Experimental Officer, Department of Mechanical Engineering said: “We chose the Moog Portable Test Controller because it is much more versatile and flexible than others on the market. It has also enabled us to progressively upgrade all our equipment to meet new challenges brought to us by our customers. Our experience with the Portable Test Controller has been highly successful and we are ordering additional equipment from Moog”.
Appendix 1: Overview Moog Portable Test Controller
The Portable Test Controller was designed based on input from customers of leading test laboratories, making it the ideal choice for simple, efficient operation in an array of testing applications. Some advantages of the Moog Portable Test Controller include unsurpassed flexibility for user-friendly, cost-effective operation in a range of testing applications, advanced safety checks built-in to ensure protection of the test article and test data and high-performance operation for both basic and complex applications. With more than 5,000 control channels installed and used daily in test labs around the world, it is a proven choice for test professionals.
Key Features
- Advanced control that is expandable up to four channels
- A portable and stand-alone test controller
- Precision control loops (e.g. force, displacement and acceleration) developed by Moog for faster and more efficient testing and reduced set-up time
- Simple operation that allows you to add just the functionality you need for cost-effective integration
- Built-in data-acquisition, integrated oscilloscope display and data storage capability on a local hard-disk, make testing easier and saving both lab space and running costs
- Compatible with any hydraulic, electric or pneumatic actuators adds to
- Easily works with all connectors for cost-effective, immediate integration
- Pseudo channel capability allowing the user to create online calculated channels using formulas and other inputs, offering greater flexibility and cost savings for the lab
- Matrix control provides measurement and control flexibility for more efficient testing
- Dual mode, bumpless switching (e.g. Force, Position) to take advantage of the full range of application
- Online adaptive control for amplitude and phase saves set-up time
- Calibration and tuning wizard to facilitate and accelerate setup.
- Expandable to 32 channels test controller version, using multiple units.
Author
Paul Garner has been with Moog since the acquisition of FCS in 2005 in the capacity of Senior Sales and Applications Engineer. Prior to joining FCS he has worked extensively in the test industry for MTS and others. Paul studied Mechanical Engineering at Wolverhampton Polytechnic and computer technology at the Open University.