Electro-hydrostatic actuators (EHA), widely used in the aerospace industry, are opening new possibilities for machine builders because they combine the best of electro-mechanical and electro-hydraulic technologies. Moog developed an EHA (see Figure 1) that is ideal for many industrial applications and competitive with traditional hydraulic solutions, lowering energy and investment costs. This technology is now proven in some very demanding industrial applications and is generating increased attention from design engineers and machine builders around the world.
Here are five compelling reasons that machine builders are evaluating EHA for new generation machines.
- Significant energy savings - Using EHA technology saves a substantial amount of energy via power on demand, while the dynamic performance is similar to conventional electro-hydraulic (EH) or electro-mechanical (EM) systems
- High forces without the need for a mechanical gearbox - For those motion control axes that require higher forces and therefore a high gearbox ratio, EHA is an attractive solution
- Power density - The power capacity and power density of an EHA can be higher than that of an Electro-Mechanical solution, as it allows machine builders to create higher forces in a given envelope size
- Fail-safe functionality - Can be easily integrated into an EHA with the same functionality and flexibility known from EH systems
- Easily integrated into existing infrastructure - Best of both technologies means machine builders can use EHA for machines that otherwise use EM actuation and the system design eliminates traditional hydraulic infrastructure, saving space and costs
What is an EHA?
The EHA converts power from electric to hydraulic to mechanical. An electric servo motor drives a bi-directional, variable speed pump connected to the two chambers of a hydraulic cylinder. Depending on the direction of the flow, the axis extends or retracts. In contrast to a hydraulic system, the power control is done by the pump. Varying the speed of the pump means varying the flow or the pressure, and thus the hydraulic power. This enables the electro-hydrostatic actuator to efficiently use energy and deliver power on demand. Figure 2 compares traditional electro-mechanical, electro-hydraulic and electro-hydrostatic actuation.
The benefits of EHA
There are numerous benefits to incorporating an EHA in a machine design. Some advantages are evident when comparing it to a traditional hydraulic systems and others to an all-electric systems. In this article, we will focus on specific ways machine builders will benefit from lower total cost of ownership, a flexible design concept and simpler maintenance.
Total cost of ownership involves a variety of contributing factors and EHA technology impacts several key elements. Energy efficiency is a natural focus for cost savings, especially in industries with the high cost of operating machines on a 24/7 basis. One of the clear advantages of EHA versus a traditional hydraulic machine is that it uses significantly less energy due to its compact, modular design with a self-contained hydraulic system and its principle of using power on demand. In addition, it does not use throttle valves, thereby reducing the heating in the system and minimizing the cooling effort needed. Convection cooling is usually sufficient for an EHA. Discussed in the section below, energy savings of nearly 30% was observed in the objective test between EHA and traditional hydraulic technologies in the die cushion press (Figure 3) conducted by Dresden University.
Designing a machine with EHA leads to a more flexible motion control concept because the EHA can handle high force without mechanical gearing. It is compact and self-contained which saves space within the machine. The system is flexible, offering various layouts and the ability to operate several axes, if done in sequence. It also delivers impressive repeatable, dynamic performance which leads to high productivity and yield. In the Dresden University test for example, the dynamic performance matched the conventional hydraulic technology even in a challenging die cushion application. Furthermore, the EHA is proven to be robust and reliable even in conditions with high shock load, leading to high machine reliability and uptime.
From a plant operation standpoint, the EHA offers easy integration and commissioning via the all-digital control that eliminates unpredictability due to temperature drift and signal noise. The digital system allows exact repeatability between several systems by replicating digital parameters without the need for tuning used in conventional systems. It allows remote access for diagnostics and maintenance. There are also numerous advantages derived from eliminating the hydraulic infrastructure and using a self-contained system. In this system there is no need for housings, couplings or external pumps and there is easy access to routine maintenance items such as filter, sensors and valves. Operational issues associated with the degradation and aging of oil in EH solutions are also mitigated as the oil is never exposed to the external environment.
Energy efficiency of EHA vs traditional hydraulics
evaluated by Dresden University
Moog’s aerospace organization has extensive experience with EHA technology. Moog also proved out the industrial viability of the design with a number of customers. What was missing was some comparative data with an existing application. To obtain this, Moog worked with Dresden University to incorporate the EHA on a die cushion press so it could be objectively compared to a traditional control system using servo valves (See Figure 4). This example is valuable as it involves high forces in a traditionally hydraulics- only application.
Die cushion presses normally have a capacity of 24 to 4,000 tons and perform a wide range of stamping operations in automotive plants including handling new materials and complex shapes such as external and internal body panels for doors, fenders, roofs and hoods. The test comparing EHA and traditional hydraulic presses was performed by the professors and students at Dresden University in conjunction with Moog to measure dynamics and energy efficiency.
The conventional system was a hydraulic press machine and the architecture for the die cushion actuation was four separate cylinders, each controlled via servo valves. All of these four axes were supplied by a variable displacement pump. Next an EHA system was installed for each cylinder in the die cushion including a servo electric motor connected with a radial piston pump. All of the four axes were connected with an accumulator to support the low pressure level. During the deep drawing process the servo motor/pump unit was acting in generator mode. Via the servo drive, it was possible to feedback the recovered energy from the die cushion to the ram actuator.
According to Professor Weber at Dresden University, “Energy savings during a complete machine cycle of approximately 30% could be achieved during tests while maintaining comparable dynamics and pressure control functionality. A 30% energy efficiency experienced by the EHA solution is a dramatic improvement especially when you consider the large amount of energy used by these kinds of machines in a single year. A future advantage is the substantial reduction or even substitution of oil cooling due to elimination of throttle losses. This test suggests EHA technology is a viable alternative motion control system from a performance standpoint with the advantage of impressive energy efficiency.” (See Figure 5) (Helbig, A. (2014). Electro-Hydrostatic Actuation: A New Energy-Efficient Option for Machine Builders, Moog White Paper, p. 1-8)
Assessing machine suitability for EHA
Evaluating if an EHA is suitable for a machine control application requires assessing the application and performance requirements. Machines that require a relatively small number of hydraulic axes are generally excellent candidates for EHA. From a “black-box perspective,” an EHA functions similarly to an EM solution. From the perspective of the automation controller (PLC in most cases), the interfaces are identical where motion profiles are planned through digital interfaces. There are two scenarios that offer the ideal application for an EHA:
- EM machine conversions that need the force capability or power density of hydraulics for a small
number of axes - All hydraulic machines that have only one or two axes of motion
Moog helps machine builders incorporate EHA technology into a new generation of machines and will assess your unique requirements. It is not always required to offer a complete standard EHA design so Moog also has a modular, building-block approach (see Figure 6). Moog combines standard building blocks such as servo drives and a servo motor/pump combinations in typical sizes with a manifold and cylinder that designers can customize to an application’s exact needs.
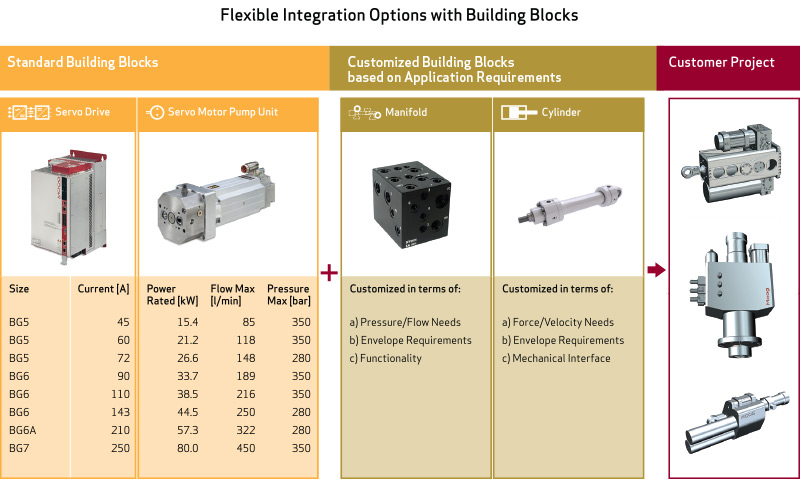
Figure 6: Moog offers a wide range of standard building block products that can be combined with other customized products to deliver electro-hydrostatic actuation solutions that fit the customer’s needs
Conclusion
Using EHA technology saves a substantial amount of energy via power on demand, while the dynamic performance is comparable to conventional EH or EM servo systems. Such a self-contained system enables a decentralized machine design, which optimizes axis performance and eliminates hydraulic infrastructure when compared with traditional hydraulic systems. When combined with electric machines, machine builders can use the EHA without incurring integration hurdles. It is easy to install because the interfaces are identical to EM solutions. In addition, the functionality is more flexible and the achievable forces are greater than traditional electric systems.
Is it time to consider EHA? Its impressive energy savings potential, ability to provide high forces without a mechanical gearbox, and easy integration and maintainability make EHA technology a clear alternative to traditional servo solutions. Call us today or learn more by reading our white paper .
Author
Achim Helbig has been with Moog since 2004 in the position of Senior Applications Engineer, Team Manager Hydraulic Systems and Innovations Project Manager. Prior to joining Moog, he worked at Dresden University and completed his Ph.D.