By Craig Jackson | February 26, 2022 - Click here to view article in Offshore Magazine Online
High-pressure, high-temperature oil wells create a challenging design environment for applications like directional drilling, so engineers should make motion control a top consideration. The conditions in which downhole tools ply their trade often reach 200°C and 35,000 psi. Motion-control technologies are a linchpin for helping oilfield services firms precisely hit a target depth or lateral position. But designing for precision is not enough. That’s because the speed and reliability of downhole equipment like rotary steering systems (RSS) and measuring tools impacts profitability.
While there are numerous off-the-shelf components for engineers to use when designing, say, an RSS, the actuation method that turns an eccentric collar and ultimately points the drill bit is what maximizes steering to accurately hit oil, instead of water or sand. In the oil and gas industry, electro-hydraulic motion control technology presents environmental and performance challenges like fluid contamination or leakage of hydraulic fluid. Oil companies and operators are increasingly looking to remove systems and tools that rely on hydraulic motion-control and instead adopt electro-mechanical technology, which typically offers higher efficiencies and advanced closed-loop control.
Take, for example, the design of subsurface safety valves (SSSV), which close production conduits in an emergency. The SSSV is a flapper valve positioned a hundred feet below the mud line; it’s critical and designed to last 20 years. Unlike SSSVs with EH actuation systems relying on HPU and hydraulic fluid coursing through multiple umbilical lines, subsurface safety valves using either electro-hydrostatic actuation or electro-mechanical actuation tap electric power to trigger the valve’s safety function. While EHA systems are ideal for constant high-force outputs, designers might also consider electric mechanical actuators for mid-range force loads with high peaks of short durations.
Below are several tips for machine designers to consider when constructing the downhole equipment that the oil and gas industry relies on for exploration and production.
Tip No. 1: Close the control loop
Closed-loop motor control systems tell equipment operators if their downhole equipment’s motor is spinning at the intended rate. A Hall effect sensor, which, among other things, detects speed and current in applications, is a simple way to close a control loop. If an application requires less precision, Hall effect sensors are a cost-effective solution. The ability to use Hall effect devices generally tops out at temperatures of 175°C.
Another method is a resolver. For rotary motion, a resolver is a highly effective way to gain rotational accuracy less than one degree. Design engineers can integrate a resolver into a brushless DC motor and steer currents and/or voltages to achieve optimum motor torque. If an application also uses a gearbox, then an engineer can add a resolver to the output shaft for additional position feedback loops.
For less precise applications such as hydraulics pumps, which may be used for closed loop lubrication of bearings or high-pressure actuation, design engineers might consider “sensorless” or open loop controls. This approach reduces the complexity of the hardware, but the simpler configuration spells reduced startup torque and potentially lower operational efficiency.
For linear applications, design engineers can consider linear variable differential transducers to collect feedback. An additional solution for closing the control loop is current feedback, which constantly monitors the amount of motor amperage to calculate the motion system force.
Tip No. 2: Drill into your motion profile and duty cycle
The first step to designing a motion control system for hardware such as valves, hydraulic pumps, eccentric steering devices or other mechanisms operating in a downhole environment is to look at the application’s motion profile. Is the tool’s motion profile rotary or linear? Is the equipment continually rotating, or does it stop after a certain number of degrees? What type of load does the motion system drive?
Next, get a handle on the application’s duty cycle. Understanding how long a mechanism or system sustains normal and peak forces or hard stops will help an engineer or operator calculate the load on the system. If the tool experiences back-and-forth motion when operating, there may be significant inertia loads on, for example, the drivetrain. While continually rotating applications often equate to straight-forward designs, there can be external factors that create a dynamic load. Accounting for these variables will help a machine designer create a robust motion control system.
Tip No. 3: Accommodating design factors, timelines
There once was a customer that had a downhole actuator, which complemented the process operators used to set plugs in their wells. We engineered a way to electromechanically retract the rod and set a packer. That EM solution required ball screws rated for 100,000 lbf in a package with an outer diameter of less than 4.5 inches. Design life for ball screws is often targeted in the millions of cycles. This application only required hundreds of cycles, so we could push the design to greater loads due to the significantly shorter life requirements. That said, there was still significant engineering effort and material upgrades to achieve these high loads in such a tight package. Design engineers should consider performance versus life expectancy due to the extreme nature of downhole applications. For instance, an engineering team can increase loads, but this could potentially reduce the tool’s life from 2,000 hours to 300 hours. To achieve optimum designs, equipment buyers and designers should be open to a range of technologies. For some high-force, compact solutions, a hydraulic motion-control system might be best, whereas electric mechanical actuators, as described above, might make sense elsewhere.
The nature of the oil and gas industry often necessitates speedy product development. But that’s not always possible when you need to design a downhole tool to last 20 years. How can engineers do the proper analysis when they may have a short timeframe in which to test? While you can accelerate testing for what an electronic board might experience over the course of 20 years, that’s not so easy with mechanical components. In those cases, engineers can look at their (or a business partner’s) component database to help assess meantime between failure data for similar components and extrapolate how long, for instance, a ball screw would last. That helps an engineer design for a long life despite tight production schedules.
The author
Craig Jackson is sales manager for the Oil & Gas division of Moog Inc.
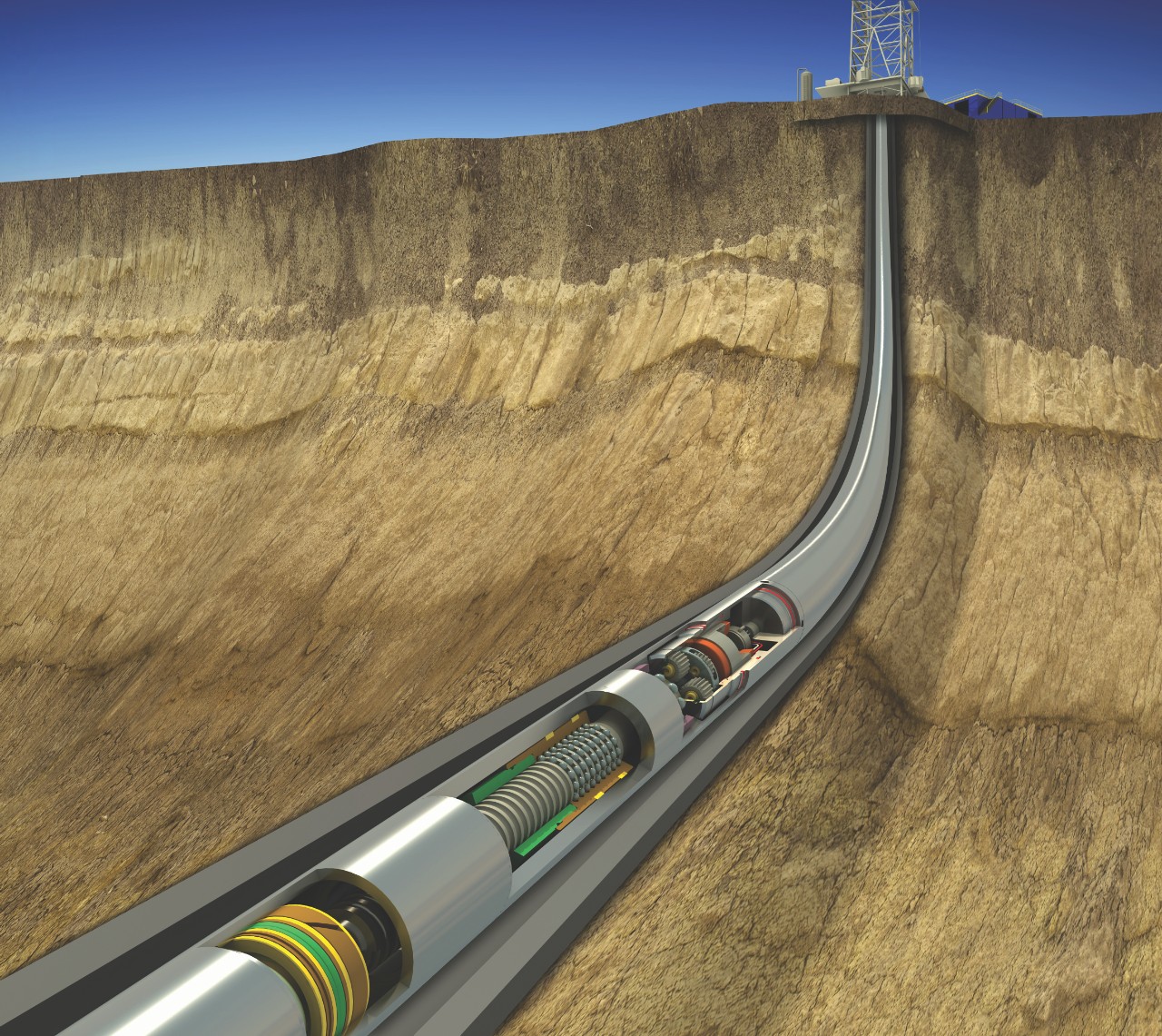
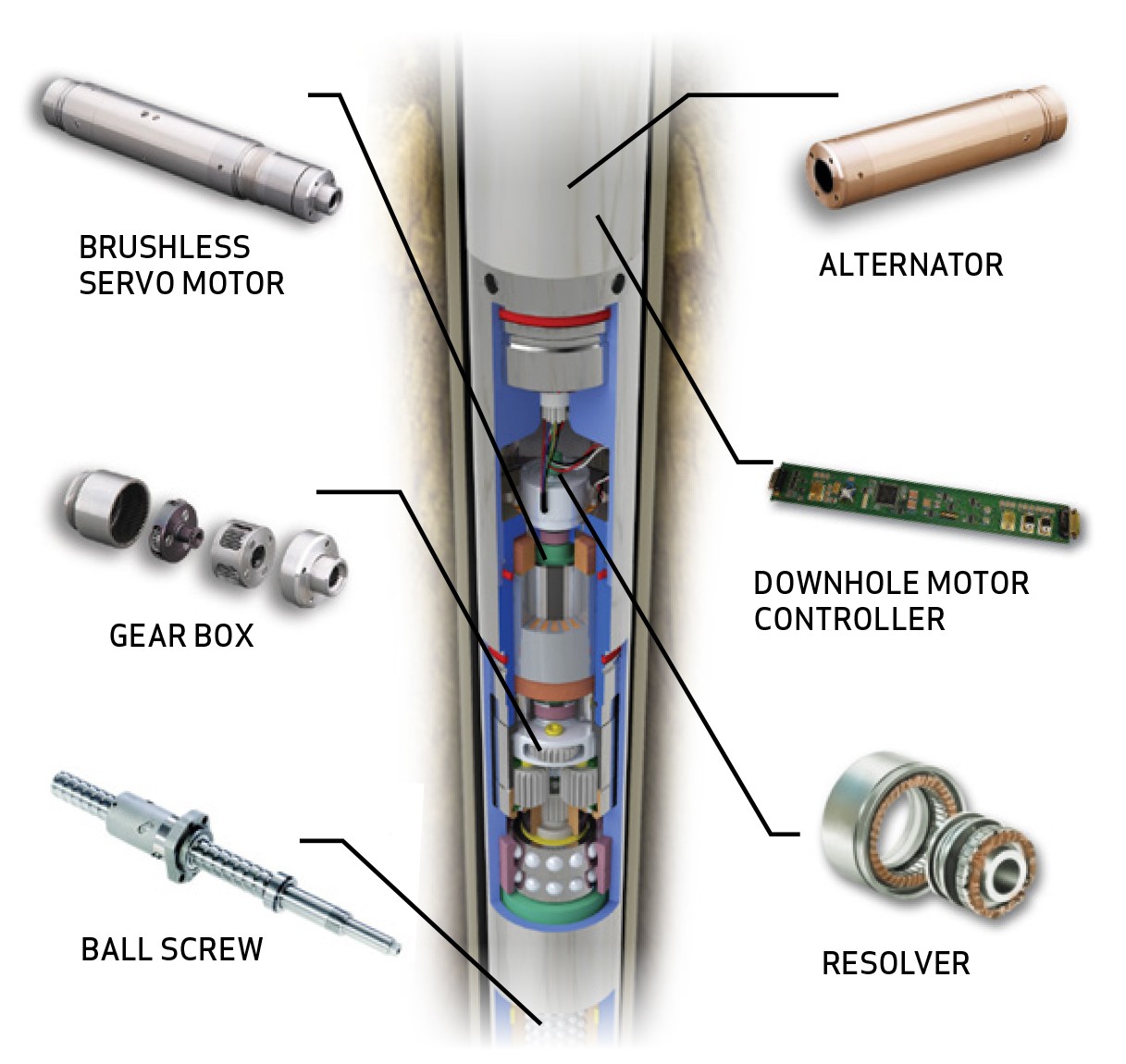
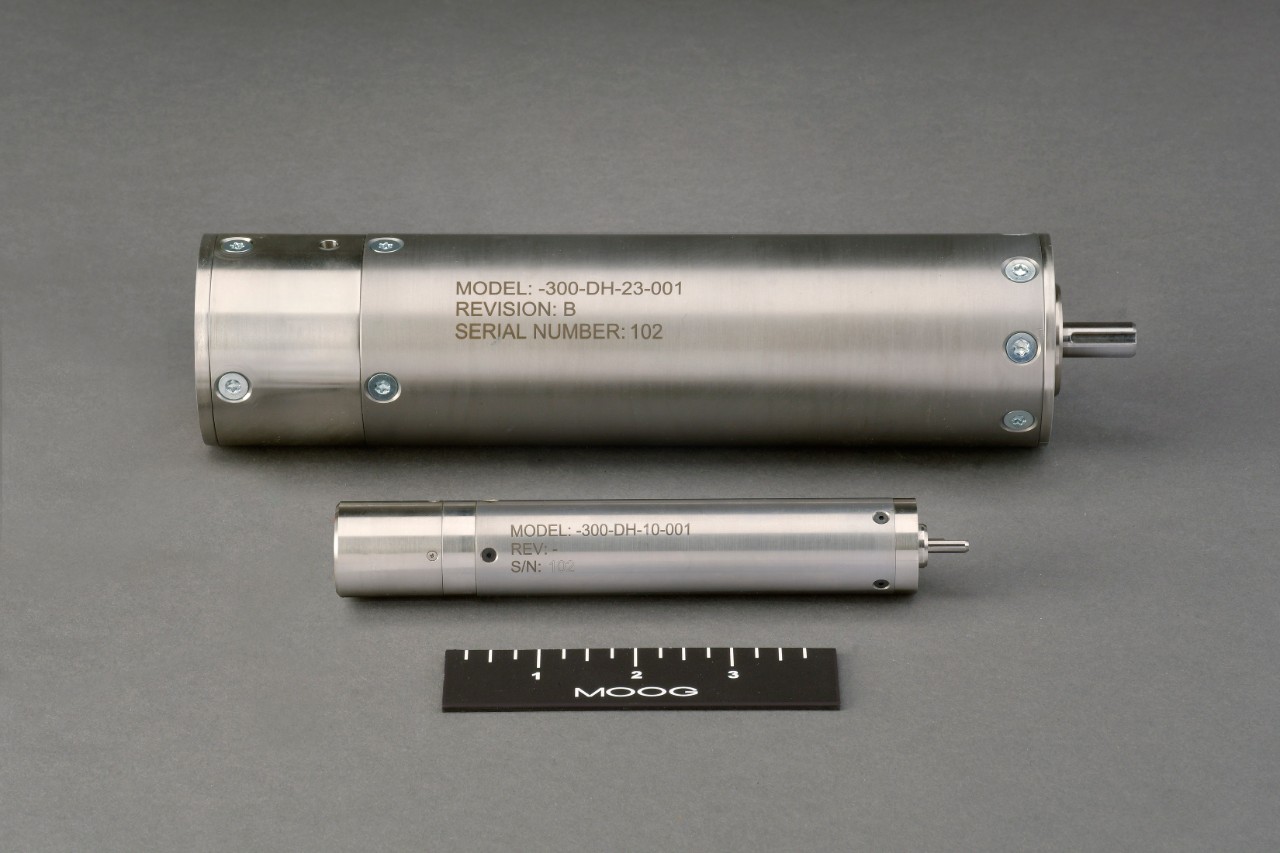
About Moog Inc.
Moog Inc. is a worldwide designer, manufacturer and integrator of precision control components and systems. Moog Industrial Group designs and manufactures high performance motion control products, solutions and services combining electric, hydraulic, and hybrid technologies with expert consultative support in a range of applications in energy, industrial machinery, simulation and test markets. We help performance-driven companies to design and develop their next-generation equipment. Moog Industrial Group, with fiscal year 2020 sales of US $909 million and over 40 locations worldwide, is part of Moog Inc. (NYSE: MOG.A and MOG.B), which had fiscal year 2020 sales of US $2.9 billion. For more information, please visit www.moog.com and www.moogsimulation.com. For career opportunities, go to www.moog.com/careers.