Gravity Offloaders for Zero Gravity Simulation
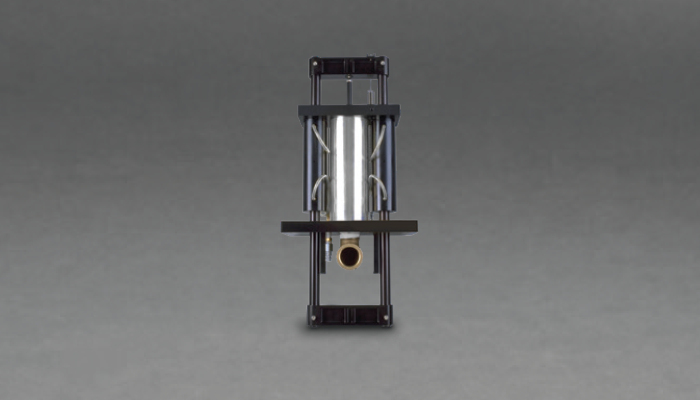
Overview
Moog’s no-sag gravity offload systems provide low frequency suspension, with modes as low as 0.1 Hz, enabling you to test and validate fixed and moving space structures before flight. All other gravity offloading methods suffer from significant limitations that prevent them from accurately simulating unconstrained (free-free) boundary conditions.
Key Features
- Wide Payload Range
- Very Low Stiffness
- Zero Static Sag
- Low Added Mass
- Frictionless
- Vibration Modes Above Test Range
Gravity Offloaders
Moog’s gravity offloaders, based on frictionless air bearing and air piston technology, provide high fidelity simulation of the space environment. They offer a wide payload range, very low stiffness, zero static deflection, and zero friction while conventional offloader technologies suffer from suspension stiffness, added mass, friction, or vibrational modes of the suspension devices, themselves. Typical systems combine three to five identical offloader devices although this quantity can be much greater for large, flexible test articles.
Applications
- Dynamic testing of space structures without changing free-free vibration modes
- Investigate effects of exercise on human health in space
- Assembly or alignment of precision structures or optical systems
- Need to apply a large force through very low stiffness such as pre-loading a test article
- Vibration isolation for airborne optics
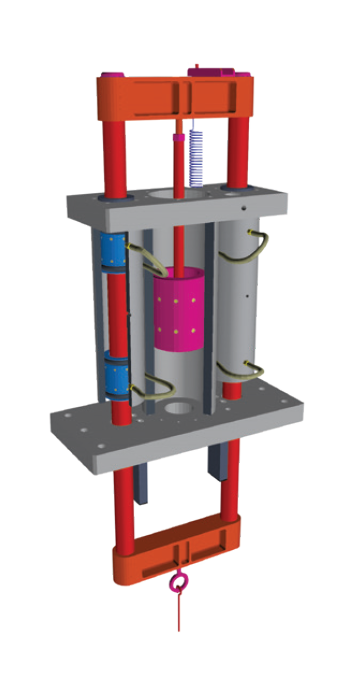
Performance
Model | AGM | AGM-A |
Payload capacity | 5 – 1500 lbs | 10 – 1500 lbs |
Typical vertical suspension frequency | 0.1 – 0.2 Hz | 0.1 – 0.2 Hz |
Vertical stroke | 0.5 to 18" | 0.5 to 18" |
Moving mass | 6 lbs. | 9 lbs. (w/o mass cancelling) 1.4 lbs. (w/ mass cancelling) |
Air spring stiffness | Payload-dependent | Payload-dependent |
Friction | <0.005% of payload weight | <0.005% of payload weight |
Dimensions (L W H) | 12.0" x 5.5" x 27.8" | 12.5" x 7.5" x 28.6" |
Air consumption at max payload | 1.5 SCFM | 1.8 SCFM |
Air supply pressure | 20 – 140 psig | 20 – 140 psig |
Electrical power | 0.5A @ 120 VAC (w/ optional displacement sensor) |
0.5A @ 120 VAC |
Electronics and software | None | Control software and electronics for active force trim control |
Moog has built and delivered well over 100 gravity offload devices of at least 10 distinct designs over multiple decades.
Available Options
- Active load leveling
- Vacuum compatible
- Mass cancellation
- Support weight from above or below
- Custom stroke or payload mass.
Walking Gravity Offloaders
Moving or deployable structures can be gravity offloaded with a “walking” version of our zero gravity suspension devices. This fully integrated solution utilizes closed loop horizontal payload tracking ability to follow a payload translating under its own power in all three directions. Tip-tilt sensors on the payload attachment cable allow the offloader position to be maintained directly over the top of the payload attachment point to minimize side loads imparted into the test article.
Applications
- Solar panel deployment testing
- Deployable booms or ion thrusters
- Torque motor characterization in space environments
- Robotic arm testing
- Walking human subjects
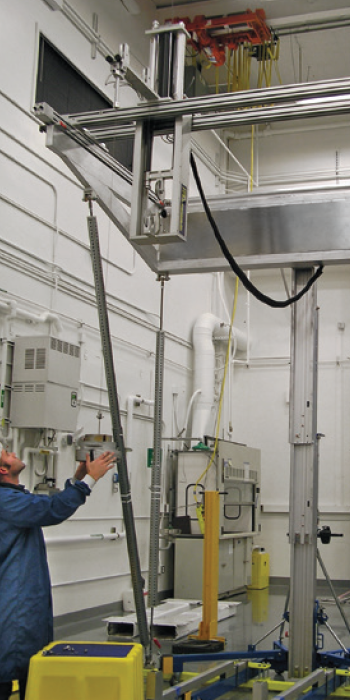
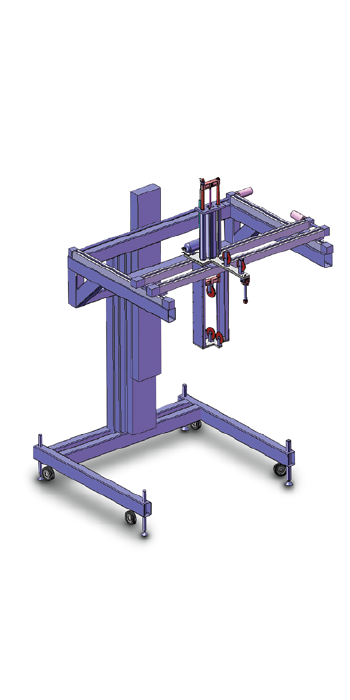
Performance
Model | WAGM-S | WAGM-L |
Payload capacity | 5 – 200 lbs | 10 – 275 lbs |
Typical vertical suspension frequency | 0.1 – 0.2 Hz | 0.1 – 0.2 Hz |
Total range of motion (X Y Z) | 78" x 51" x 69" | 164" x 95" x 54" |
Moving mass | 1 lbs | 5 lbs |
Air spring stiffness | Payload-dependent | Payload-dependent |
Vertical force error | 0.1 – 0.3% of payload weight typical | 0.1 – 0.5% of payload weight typical |
Horizontal force error | 0.1 – 0.5% of payload weight typical | 0.1 – 0.5% of payload weight typical |
Air consumption at max payload | 1.5 SCFM | 1.8 SCFM |
Air supply pressure | 20 – 120 psig | 20 – 120 psig |
Electrical power | 10A @ 120 VAC | 20A @ 208 VAC 3Ø 5A @ 120 VAC |
Electronics and software | Control software and electronics for active horizontal tracking |
Control software and electronics for active tracking in all axes |
Note: These configurations are typical examples. Numerous variations and options are possible and requests for custom versions are welcome.
What Makes Moog's Gravity Offloaders Superior?
An ideal gravity offload system has the following features: wide payload range, no vertical stiffness, no static sag, no added moving mass, no friction, and no added vibration modes within the frequency range of interest. Moog’s proprietary pneumatic suspension devices excel in all six of these categories while alternative offloader approaches suffer significantly in one or more areas and corrupt measurements of low frequency modes.
Performance
Alternative Offloader Technology | Limitations |
Water bouyancy systems | High viscous damping |
Excessive vertical stiffness | |
Air bouyancy systems (e.g. helium) | Adds minimum of 16% of payload mass |
Overhead air bearing or ball bearing dollies | Artificially constrains vertical degree of freedom |
Imposes artificial lateral drag forces | |
Suspension cable systems (e.g. cable in series with linear spring) | Very low stiffness required of spring introduces large static sag |
Only practical for vertical displacements on the order of inches, not adequate for deployment testing | |
Cables with pullies and offload weights | Friction from cable-pulley assemblies introduces non-linearities |
Tuning can be challenging | |
Bungee cords | Static sag of 82 ft required for 0.1 Hz system |
Air bearing tables | Does not support vertical motions |
Significantly restricts angular motions |