Hexapods & Positioning Systems
Moog’s 6-axis hexapods, also known as Stewart platforms, are parallel kinematic robotic systems capable of positioning or moving a payload in all six degrees of freedom (6-DOF): lateral, longitudinal, and vertical translations as well as roll, pitch, and yaw rotations. These 6-DOF hexapods can move simultaneously in multiple axes or independently in a single axis while preventing movement in the other axes. A hexapod’s parallel linear actuator arrangement provides high load capacity, stiffness, and accuracy compared to serial robotic manipulator architectures. Other motion control devices typically provide positioning, motion simulation, or vibration isolation in only one or two degrees of freedom making Moog’s high-performance hexapods the ideal solution when multi-axis motion is desired.
Moog’s hexapods are provided as a turnkey system complete with 6-DOF controller, software, and cabling. The control software allows for a programmable pivot point so the effective center of rotation of the hexapod’s motion can coincide with the desired location for any application. A simple and intuitive graphical user interface (GUI) allows a user to configure and operate a Moog hexapod within minutes. Cleanroom and vacuum-compatible versions are available as well as custom hexapods and multi-axis stages.
Custom Systems
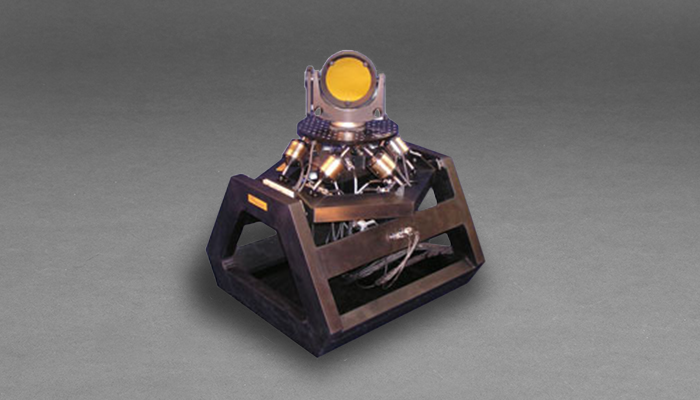
Sometimes the hexapod needs to match the application rather than trying to make the application match the hexapod. We are able and willing to modify our standard hexapods to meet specific customer requirements including extreme environments. For unique applications, we also build custom hexapods that leverage off our heritage designs. If you cannot find a standard hexapod that meets your needs, please contact our engineering team to discuss.
Space Test Simulation Solutions
Vibration Isolation Benches
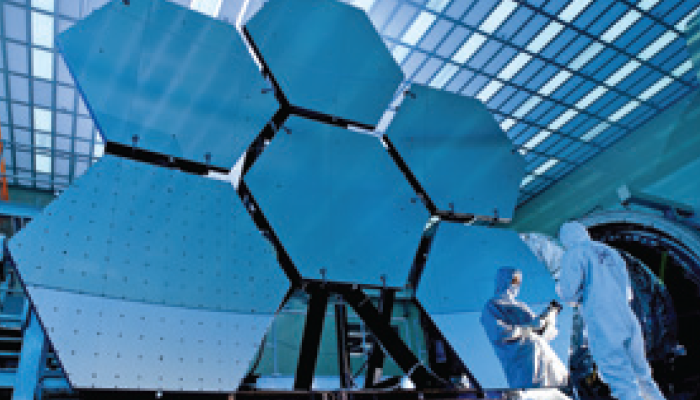
Ultra-precise metrology systems and test facilities for large space optics require extremely stable, quiet environments. Moog’s vibration isolation benches mechanically decouple the bench from facility disturbance sources including pumps, machinery, or nearby vehicle traffic.
Gravity Offloaders for Zero Gravity Simulation
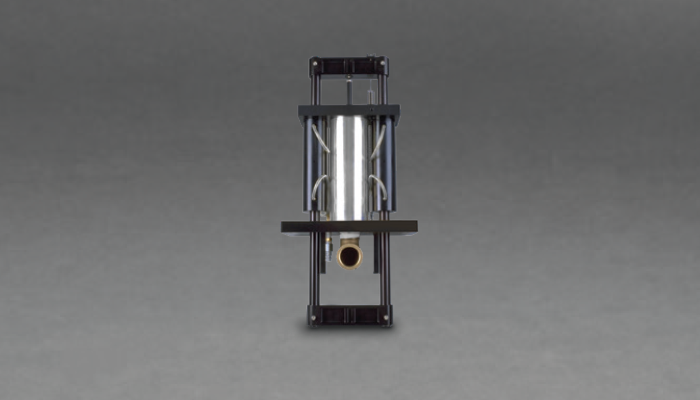
Gravity influences structures differently on orbit, but those structures must be integrated and validated on the ground. A deployable spacecraft appendage is often mass-optimized for zero gravity performance but unable to support its own weight on Earth.